Extol
Plastic Welding
Plastic welding is the process of heating two pieces of plastic and pressing them together until they fuse.
There are several different types of plastic welding. Each technology differs in how it applies heat and pressure to the parts, but the basic steps are the same—add heat, apply pressure, and cool. Plastic welds are strong molecular bonds. Depending on which welding technology is used, the weld is hermetically sealed.
Extol is a manufacturing technology company that improves the way plastic products are made.
We provide plastic assembly technology, custom automation, and engineering services across our customers’ value stream.
Hot-plate welding is the process of welding two plastic parts together using a heated tooling plate. A weld rib or bead on each component is brought into contact with the hot plate. Heat conducts into the weld rib, causing it to melt. The heated tool is then removed, and the parts are pushed together until they bond to one another.
IR welding is a non-contact welding process that joins two plastic parts together with IR energy. IR emitters heat a weld rib or bead on each component. The IR source is removed, and the parts are pushed together until they are welded.
Laser welding uses a precise IR laser beam directed through a transmissive material and penetrated into an absorptive material. The two materials are held in tight contact with each other, and the joint between them heats up and melts as energy from the laser is absorbed. The result is a clean weld with minimal flash.
Plastic staking is a method of joining components together that uses a molded stud or boss to mechanically retain a mating component. Heat is applied to the boss, softening it. A forming tool is then used to reshape the material into a cap or stake.
Spin welding is a method of joining plastic components together with surface friction concentrated in a circular weld joint. One part is spun relative to another and force is applied, causing the material to heat and melt. The spinning process stops and the parts continue to be pressed together while they bond together.
Why Choose Assembly Solutions for Your Next Project?
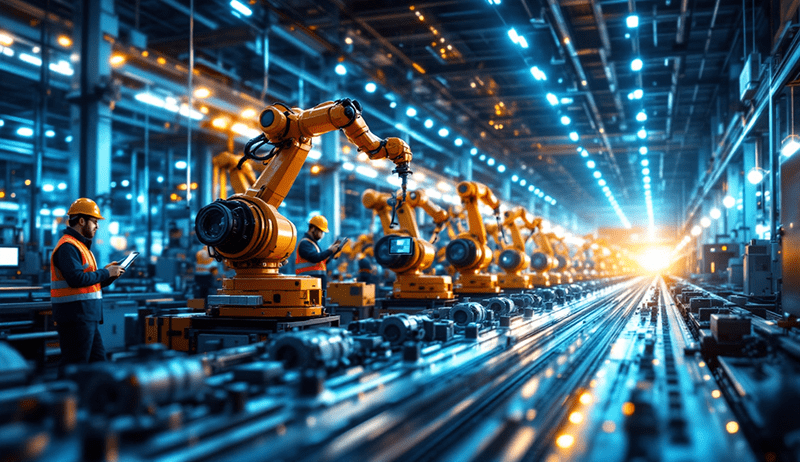
Expertise and Experience: With over thirty years of combined experience, ASI's team, led by Marty Grimes, Michael Grimes, and Rob Grimes, brings a wealth of knowledge in industrial technology applications. This expertise ensures that your project benefits from innovative solutions tailored to your specific needs.
Comprehensive Solutions: ASI represents a range of industrial technology companies, offering solutions in leak testing, plastic welding, plastic joining, screw & nut blow feed systems, clip placement feed systems, radial riveting, material handling, and part marking. This breadth of offerings means you can find multiple solutions under one roof, simplifying your sourcing process..
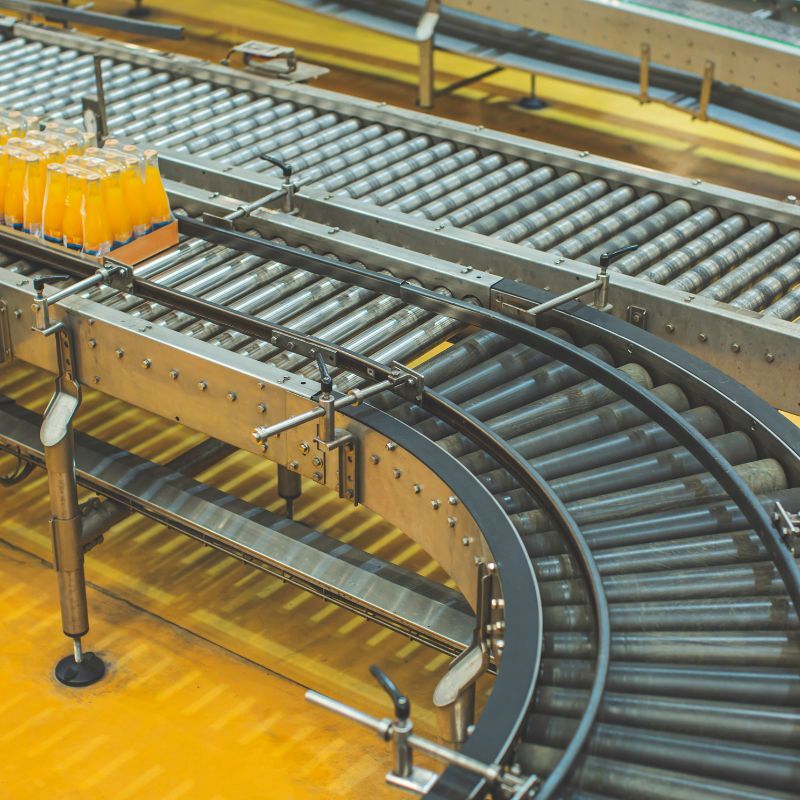
Industry Recognition: ASI's dedication to professional sales representation and continuing education is recognized through their membership in esteemed organizations like the Manufacturers and Agents National Association (MANA) and Manufacturers’ Agents of Cincinnati (MAC). This commitment to excellence ensures that you work with a company that values industry standards and best practices.
Geographical Coverage: Serving Kentucky, Southern Indiana, Southern Ohio, and Tennessee, ASI has a strong regional presence, making them an accessible and reliable partner for local businesses.
Time and Efficiency: Partnering with ASI can save you valuable time. Their automation solutions help fill in the gaps left by manual labor, increasing production throughput and allowing your team to focus on strategic planning rather than reactive problem-solving.
Support and Innovation: Clients value ASI for its timely support and the fresh ideas it brings, moving away from the 'this is how we have always done it' mindset. This approach ensures that your project benefits from the latest in manufacturing technology.